अपघर्षक ऊतक को मोटे तौर पर तीन श्रेणियों में विभाजित किया गया है: तंग, मध्यम और ढीला।प्रत्येक श्रेणी को आगे संख्याओं आदि में विभाजित किया जा सकता है, जो संगठन संख्याओं द्वारा भिन्न होते हैं।संगठन की संख्या जितनी अधिक होगीअपघर्षक उपकरण, में अपघर्षक का आयतन प्रतिशत उतना ही कम होगाअपघर्षक उपकरण, और अपघर्षक कणों के बीच का अंतर जितना अधिक होगा, जिसका अर्थ है कि संगठन उतना ही ढीला होगा।इसके विपरीत, संगठन की संख्या जितनी कम होगी, संगठन उतना ही मजबूत होगा।ढीले ऊतक वाले अपघर्षक का उपयोग करते समय निष्क्रिय करना आसान नहीं होता है, और पीसने के दौरान कम गर्मी उत्पन्न करते हैं, जो वर्कपीस के थर्मल विरूपण और जलने को कम कर सकता है।चुस्त संगठन वाले अपघर्षक उपकरण के अपघर्षक कण गिरना आसान नहीं होते हैं, जो अपघर्षक उपकरण के ज्यामितीय आकार को बनाए रखने के लिए फायदेमंद होता है।अपघर्षक उपकरण का संगठन केवल निर्माण के दौरान अपघर्षक उपकरण सूत्र के अनुसार नियंत्रित किया जाता है, और आम तौर पर मापा नहीं जाता है।सुपरब्रेसिव बॉन्डेड अपघर्षक मुख्य रूप से हीरे, क्यूबिक बोरान नाइट्राइड आदि से बने होते हैं और एक बॉन्डिंग एजेंट के साथ बंधे होते हैं।हीरे और क्यूबिक बोरॉन नाइट्राइड की ऊंची कीमत और अच्छे पहनने के प्रतिरोध के कारण, उनके साथ बने बंधुआ अपघर्षक सामान्य अपघर्षक बंधुआ अपघर्षक से भिन्न होते हैं।सुपरहार्ड अपघर्षक परत के अलावा, संक्रमण परतें और सब्सट्रेट भी होते हैं।सुपरब्रेसिव परत वह हिस्सा है जो काटने की भूमिका निभाता है, और सुपरब्रेसिव और बॉन्डिंग एजेंटों से बना होता है।मैट्रिक्स पीसने में सहायक भूमिका निभाता है और धातु, बैक्लाइट या सिरेमिक जैसी सामग्रियों से बना होता है।
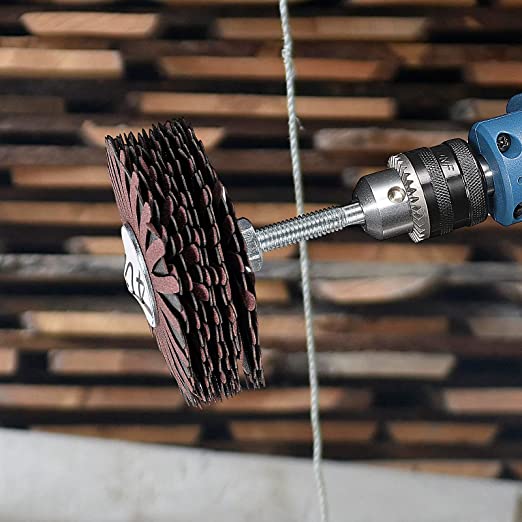
मेटल बॉन्ड अपघर्षक के लिए दो विनिर्माण प्रक्रियाएं हैं, पाउडर धातुकर्म और इलेक्ट्रोप्लेटिंग, जो मुख्य रूप से सुपरहार्ड अपघर्षक बॉन्डेड अपघर्षक के लिए उपयोग की जाती हैं।पाउडर धातुकर्म विधि में बाइंडर के रूप में कांस्य का उपयोग किया जाता है।मिश्रण के बाद, इसे गर्म दबाव या कमरे के तापमान पर दबाने से बनाया जाता है, और फिर सिंटर किया जाता है।इलेक्ट्रोप्लेटिंग विधि इलेक्ट्रोप्लेटिंग धातु के रूप में निकल या निकल-कोबाल्ट मिश्र धातु का उपयोग करती है, और अपघर्षक उपकरण बनाने के लिए इलेक्ट्रोप्लेटिंग प्रक्रिया के अनुसार सब्सट्रेट पर अपघर्षक को समेकित किया जाता है।अपघर्षक की विशेष किस्मों में सिन्जेड कोरंडम अपघर्षक और फाइबर अपघर्षक शामिल हैं।सिंटर्ड कोरंडम अपघर्षक उपकरण लगभग 1800 ℃ पर एल्यूमिना महीन पाउडर और उचित मात्रा में क्रोमियम ऑक्साइड के साथ मिश्रण, गठन और सिंटरिंग द्वारा बनाया जाता है।इस प्रकार काअपघर्षक उपकरणइसकी एक कॉम्पैक्ट संरचना और उच्च शक्ति है, और इसका उपयोग मुख्य रूप से घड़ियों, उपकरणों और अन्य भागों के प्रसंस्करण के लिए किया जाता है।फाइबर अपघर्षक उपकरण फाइबर फिलामेंट्स (जैसे नायलॉन फिलामेंट्स) से बने होते हैं जिनमें अपघर्षक पदार्थ होते हैं या उनसे चिपक जाते हैं।उनमें अच्छी लोच होती है और मुख्य रूप से धातु सामग्री और उनके उत्पादों को चमकाने के लिए उपयोग किया जाता है।
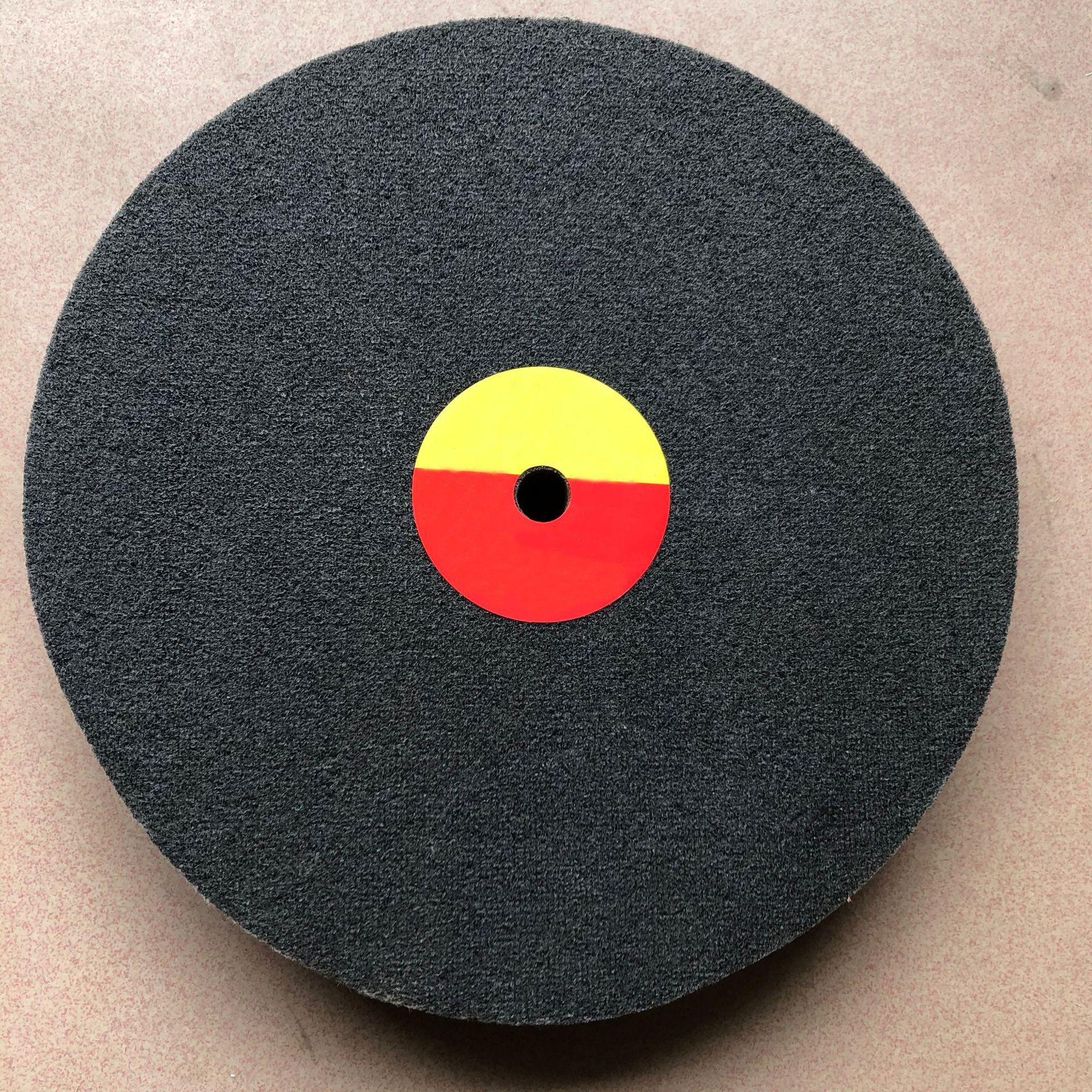
संक्रमण परत का उपयोग मैट्रिक्स और सुपरब्रेसिव परत को जोड़ने के लिए किया जाता है, और यह एक बॉन्डिंग एजेंट से बना होता है, जिसे कभी-कभी छोड़ा जा सकता है।आमतौर पर उपयोग किए जाने वाले बाइंडर रेजिन, धातु, प्लेटेड धातु और सिरेमिक हैं।
बंधुआ अपघर्षक की विनिर्माण प्रक्रिया में शामिल हैं: वितरण, मिश्रण, गठन, गर्मी उपचार, प्रसंस्करण और निरीक्षण।अलग-अलग बाइंडरों के साथ, विनिर्माण प्रक्रिया भी अलग-अलग होती है।सिरेमिक बंधनअपघर्षक उपकरण मुख्य रूप से दबाने की विधि अपनाता है।सूत्र के वजन अनुपात के अनुसार अपघर्षक और बाइंडर को तौलने के बाद, इसे समान रूप से मिश्रण करने के लिए मिक्सर में डालें, इसे धातु के सांचे में डालें, और प्रेस पर अपघर्षक उपकरण को खाली आकार दें।खाली हिस्से को सुखाया जाता है और फिर भूनने के लिए भट्टी में लोड किया जाता है, और फायरिंग तापमान आम तौर पर लगभग 1300 डिग्री सेल्सियस होता है।जब कम पिघलने वाले बिंदु वाले सिंटर बाइंडर का उपयोग किया जाता है, तो सिंटरिंग तापमान 1000°C से कम होता है।फिर इसे निर्दिष्ट आकार और आकार के अनुसार सटीक रूप से संसाधित किया जाता है, और अंत में उत्पाद का निरीक्षण किया जाता है।राल-बंधित अपघर्षक आम तौर पर कमरे के तापमान पर एक प्रेस पर बनते हैं, और गर्म-दबाने वाली प्रक्रियाएं भी होती हैं जिन्हें हीटिंग स्थितियों के तहत गर्म किया जाता है और दबाव डाला जाता है।ढलाई के बाद इसे सख्त भट्टी में सख्त किया जाता है।जब फेनोलिक राल का उपयोग बाइंडर के रूप में किया जाता है, तो इलाज का तापमान 180 ~ 200 ℃ होता है।रबर-बंधित अपघर्षक को मुख्य रूप से रोलर्स के साथ मिलाया जाता है, पतली शीट में रोल किया जाता है, और फिर छिद्रण चाकू से छिद्रित किया जाता है।मोल्डिंग के बाद, इसे 165 ~ 180 ℃ के तापमान पर वल्कनीकरण टैंक में वल्कनीकृत किया जाता है।
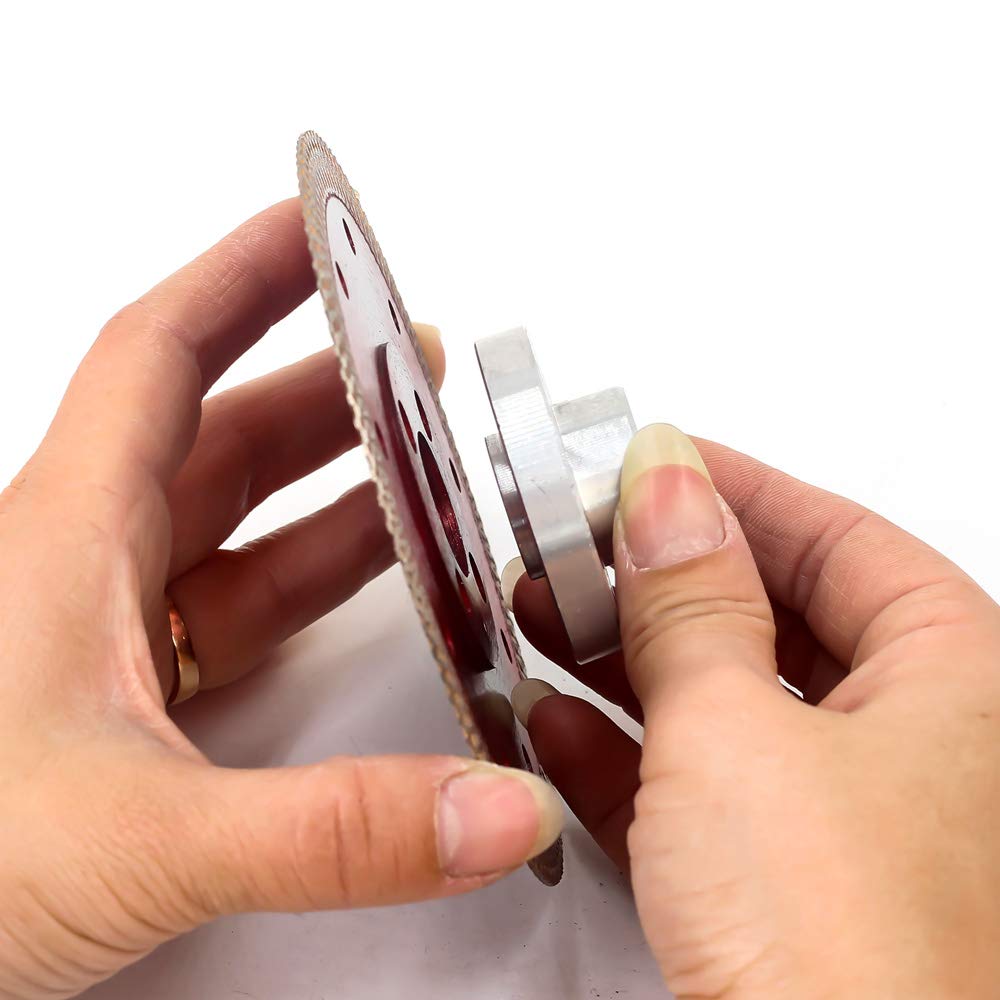
पोस्ट करने का समय: सितम्बर-05-2022